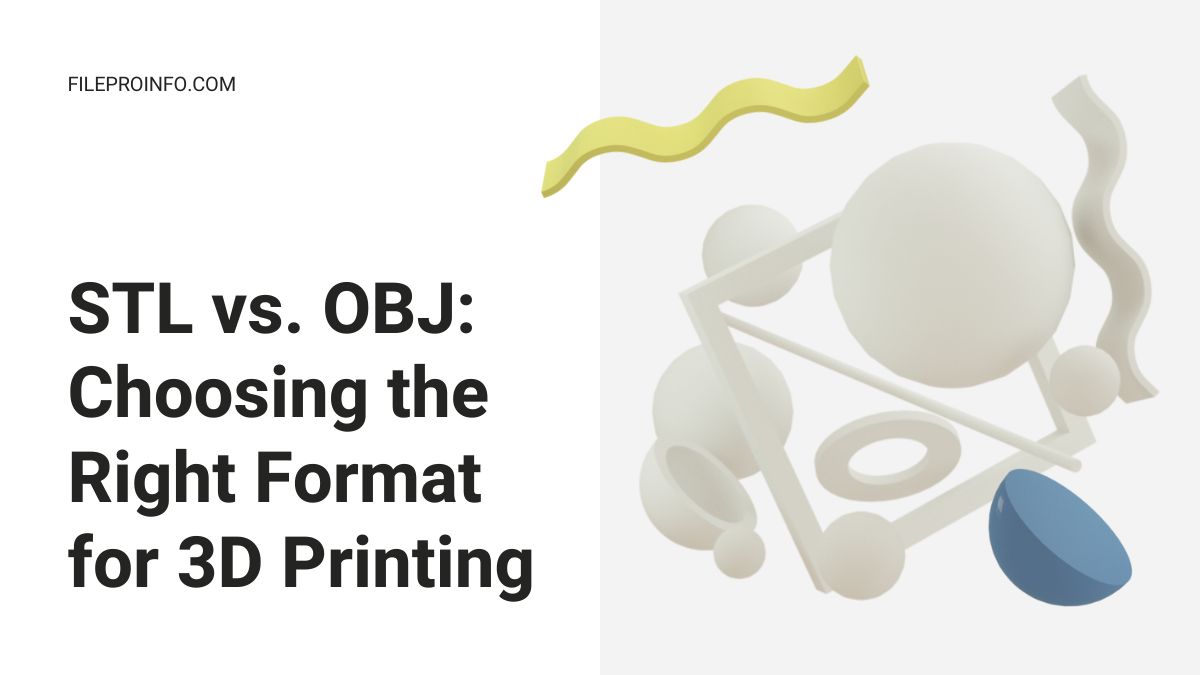
3D printing has changed manufacturing, prototyping, and creative projects. It lets people and businesses turn digital models into objects. Picking the right file format for your models is a key step in 3D printing. STL and OBJ are two of the most popular formats for 3D printing. Each has distinct characteristics, advantages, and limitations. This blog post is about the differences between STL and OBJ formats. It explains how to choose the best one for your 3D printing needs.
Understanding STL and OBJ Formats
STL Format
STL, or Stereolithography, is one of the oldest 3D printing file formats. It is also one of the most widely used. STL was created by 3D Systems in 1987. It has become the industry standard for 3D printing. This is because it is simple and works with many 3D printers and software.
Key Features of STL:
- Geometry-Based: STL files represent 3D objects using a mesh of triangles (polygons) that describe the object’s surface geometry.
- No Color or Texture: STL files contain only geometric information and do not include color, texture, or material properties.
- File Size: STL files can be relatively small because they only store geometric data, making them efficient for transferring and processing.
- Precision: STL files can represent detailed and complex geometries accurately, depending on the resolution of the mesh.
OBJ Format
OBJ is a 3D graphics format created by Wavefront Technologies in the 1980s. OBJ files can store more complex info. They are useful and popular in 3D modeling apps. These apps include 3D printing, animation, and gaming.
Key Features of OBJ:
- Geometry-Based: Similar to STL, OBJ files use a mesh of polygons to describe the object’s surface geometry. However, OBJ can support various polygon types, not just triangles.
- Supports Color and Texture: OBJ files can include color, texture maps, and material properties, providing more detailed information about the object’s appearance.
- File Size: OBJ files can be larger than STL files due to the additional information they store, such as textures and colors.
- Flexibility: OBJ files can be used for a wide range of applications beyond 3D printing, such as rendering and animation.
Comparing STL and OBJ Formats
You need to compare STL and OBJ. They differ across several key factors.
1. Geometry and Detail
- STL: STL files are excellent for capturing the geometric detail of 3D models. The resolution of the mesh can be adjusted to represent intricate details accurately. However, the simplicity of the format means it is limited to triangular polygons.
- OBJ: OBJ files offer greater flexibility in representing geometry, as they can use various polygon types (triangles, quadrilaterals, and more). This allows for more accurate models. It is also better for complex shapes.
2. Color and Texture
- STL: One of the primary limitations of STL files is their inability to store color, texture, or material information. This makes them less suitable for applications where visual appearance is important.
- OBJ: OBJ files can store color and texture maps, making them ideal for projects that require detailed visual information. This is very useful for things like gaming, animation, and detailed product design.
3. File Size and Performance
- STL: STL files are typically smaller in size compared to OBJ files because they only store geometric data. This makes them easier to transfer and faster to process in 3D printing software.
- OBJ: OBJ files can be larger due to the additional information they store. While this can provide more detail, it can also result in longer processing times and increased storage requirements.
4. Compatibility and Use Cases
- STL: As the de facto standard for 3D printing, STL files are widely supported by virtually all 3D printers and slicing software. This makes them a reliable choice for most 3D printing applications.
- OBJ: OBJ files are also supported by many 3D printers and software, but their compatibility is not as universal as STL. They are more commonly used in applications that require detailed visual information, such as rendering and animation.
Choosing the Right Format for Your 3D Printing Project
The choice depends on your project’s specific requirements. It’s between STL and OBJ for 3D printing. Here are some considerations to help you decide:
When to Use STL
- Prototyping and Functional Parts: If your primary goal is to create functional parts or prototypes without concern for color or texture, STL is the ideal choice. Its simplicity and efficiency make it perfect for these applications.
- Simplicity and Speed: If you need to quickly prepare and print a model, STL files’ smaller size and faster processing times can be advantageous.
- Compatibility: When working with a wide range of 3D printers and software, STL ensures maximum compatibility and ease of use.
When to Use OBJ
- Detailed Visual Models: If your project requires detailed visual information, such as color and texture, OBJ is the better choice. This is particularly important for applications in product design, gaming, and animation.
- Complex Geometry: When dealing with complex shapes that require more than just triangular polygons, OBJ’s flexibility in representing geometry can be beneficial.
- Multi-Use Models: If you plan to use the 3D model for purposes beyond printing, such as rendering or animation, OBJ’s ability to store additional information makes it more versatile.
Practical Tips for Working with STL and OBJ Files
Regardless of the format you choose. Here are some tips for successful 3D printing:
1. Check for Errors
Before printing, always check your STL or OBJ files for errors such as non-manifold edges, holes, or intersecting faces. Many 3D printing software packages include tools for detecting and fixing these issues.
2. Optimize the Mesh
For STL files, adjust the mesh resolution to balance detail and file size. Too high a resolution can result in unnecessarily large files, while too low a resolution can lose important details.
3. Prepare for Printing
Use slicing software to prepare your model for printing. This involves setting print parameters such as layer height, infill density, and support structures. Both STL and OBJ files can be imported into slicing software for this purpose.
4. Consider Post-Processing
After printing, post-processing techniques such as sanding, painting, or applying a finish can enhance the appearance and functionality of your printed objects. This is particularly useful for models created from OBJ files that include color and texture information.
Conclusion
Picking the right format for your 3D print project is key. It will help you get the results you want. STL and OBJ both have pros and cons. The best option depends on your project’s needs. STL is great for simple parts and prototypes. They need speed. But, OBJ is best for detailed visual models and complex geometry.
Understanding the differences between these formats is key. Also, the practical tips will let you decide well and get good 3D printing results. You may be a hobbyist, designer, or engineer. Using the right file format will let you maximize your 3D printing projects.