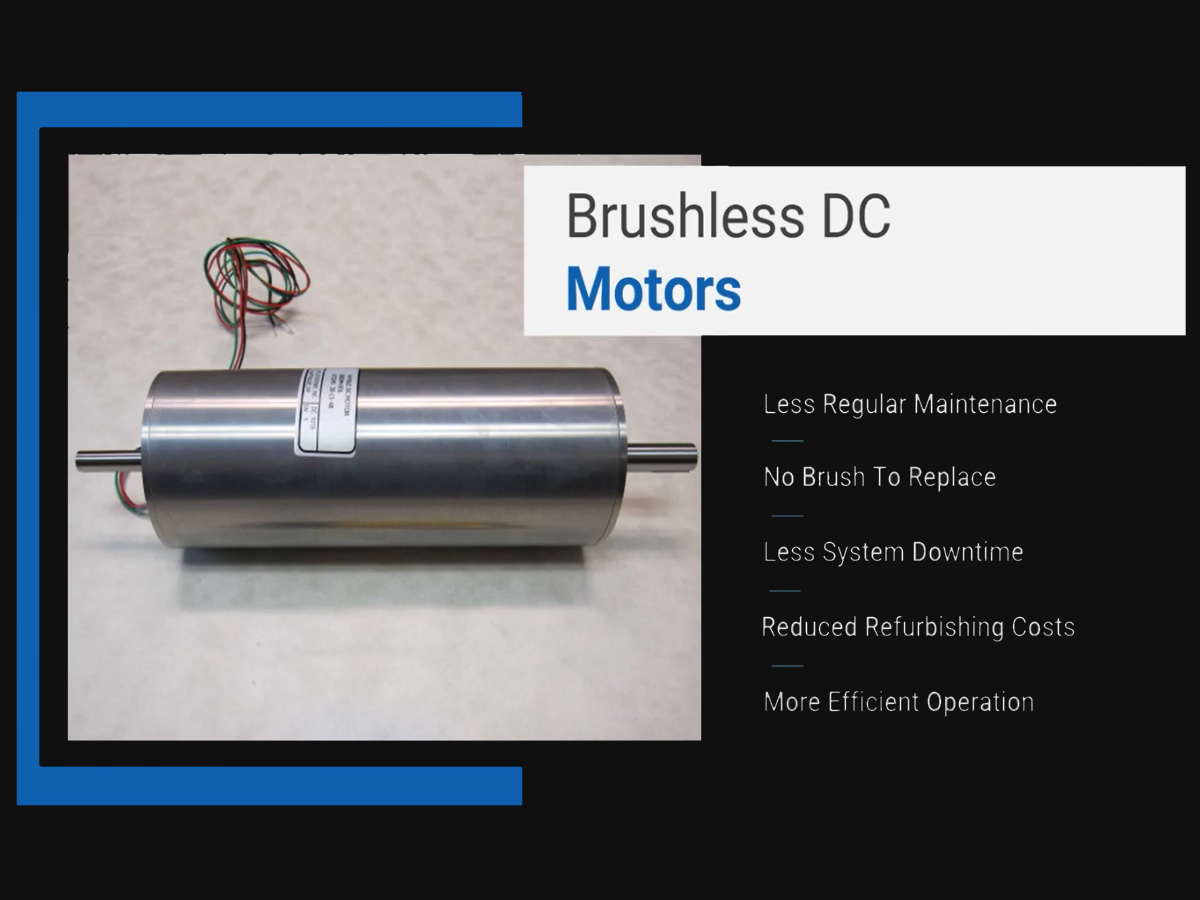
When you need a new motor, whether, for an original equipment application or to replace a unit that’s no longer operational, there are many different options to consider. Correctly identifying the most appropriate operational parameters and motor features for your application will determine how well that motor performs, how long its lasts, and whether it proves to be a reliable and high-value investment for your equipment.
.
Apart from identifying the specific type of motor, whether it’s a 400 Hz AC induction motor for an aerospace setting or brushless DC motors for heavy manufacturing needs, one of the biggest tasks is determining whether a custom motor is needed or if a standard one can meet unique needs. Addressing the following questions will help in that process.
Will The Motor Be Subject To Extreme Circumstances?
The motor you require many only needs to perform a simple job of converting electrical power into torque. But if it needs to do so in extreme temperatures, where there may be heavy vibration, high moisture, or likely exposure to dust, dirt, or other contaminants, then some special motor features may be needed.
It is possible to customize motors so that they are extra resistant to factors that otherwise compromise performance. Fortunately, a few modifications can be highly effective and seldom require that a motor be re-designed from the start.
The addition of potted coils, special winding assemblies, adjustments to various materials, and/or changes to the motor’s housing and insulation can be sufficient at improving endurance under extreme conditions. Many of these modifications can be applied without a lot of extra time and expense. Such additions can deliver major dividends, as motors with improved endurance capabilities will require less maintenance and will not need to be replaced as often as standard varieties.
Does The Motor Need To Be High-Performance?
Aerospace BLDC motors, mil-spec AC motor generators, and heavy industrial synchronous motors all need to perform with exceptional reliability. Such high-performance motors meet strict operational demands and they are usually made to specifics that determine their design, materials, and other features.
High-performance motors don’t necessarily need to be custom, and in the case of motors meant for defense and aerospace settings, certain industry and application-specific standards must be met and maintained. In such cases, a modified or customized motor might not be appropriate.
For high-performance equipment that is not subject to such standardization, motors can be made to custom parameters that will elevate their performance capabilities. As with the manufacture of motors that must operate in extreme circumstances, changes to materials, the motor’s design and assembly, and other features can significantly improve the motor’s efficiency, speed, longevity, and more.
Have Previous Standard Motors Under Performed?
In the case of standard equipment that utilizes standard motors, maintenance and replacements will be needed at one point or another. But if standard motors are continuously underperforming and replacements are needed with regular frequency, a custom motor can solve this problem.
There are a number of modifications that can amount to a significant increase in motor longevity and performance, which do not greatly alter the design of standard units. Many AC and brushless DC motor manufacturers can produce what are essentially upgraded versions of standard motors.
The problem with many commercial off-the-shelf units is their limited operational life due to standard materials and minimal standards that satisfy mass production needs. A custom version of a standard electric motor can be a high-value solution for its ability to outlast standard products that must be replaced over and over.
Choosing A Solution
There are many other factors that determine whether a standard or custom motor is better suited to a specific application. Whether you need a servo motor for a robotics prototype or a frameless BLDC motor to fit within a special assembly, it’s beneficial to submit your performance requirements to an independent motor manufacturer. Getting guidance directly from an industrial source can save time when pairing a motor with an application, which in turn will save maintenance and cost.
Learn more from technology.